SMT実装とは
SMT(Surface Mount Technology)実装は、電子部品をプリント基板の表面に直接実装する方法で、現在ではプリント基板製造において最も一般的に使用されている実装技術です。従来のスルーホール実装と異なり、部品のリードを基板の穴に通す必要がなく、基板表面のパッドに直接はんだ付けを行います。
この技術の主な特徴として以下が挙げられます。
• 部品の小型化が可能
• 基板の高密度実装に対応
• 製造コストの削減
• 生産効率の向上
• 両面実装が容易
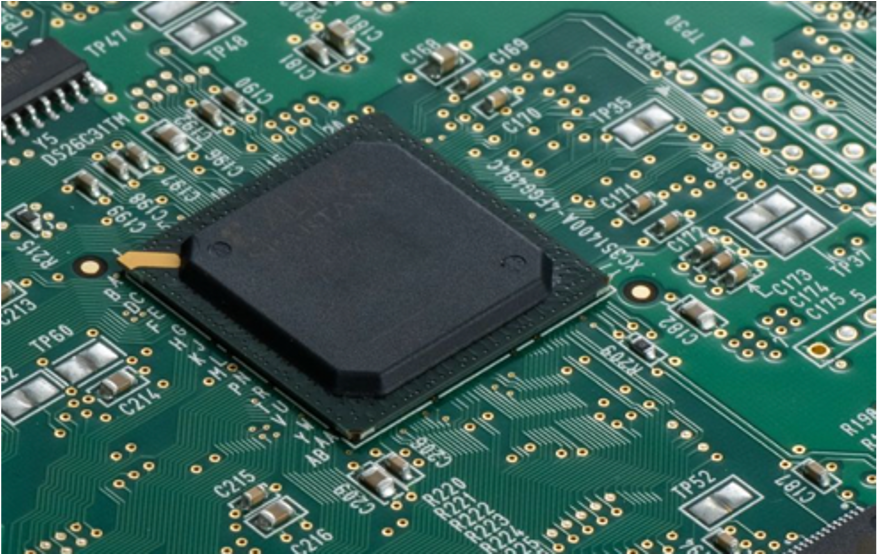
SMT実装の工程
はんだ印刷工程
SMT実装の最初の工程では、基板上の所定の位置にクリームはんだを印刷します。この工程では、メタルマスクと呼ばれる金属製の版を使用し、精密な印刷を行います。印刷品質は実装品質を大きく左右するため、以下の点に注意が必要です。
• メタルマスクの開口部設計
• スキージ圧や印刷速度の調整
• クリームはんだの粘度管理
• 印刷位置の精度確保
マウント工程
部品装着工程では、高速・高精度な自動実装機を使用して電子部品を基板上に配置します。この工程での重要なポイントは以下の通りです。
• 部品の正確な位置決め
• 適切な実装圧力の設定
• 部品の極性確認
• 実装順序の最適化
リフロー工程
実装された部品をはんだ付けするため、リフロー炉で加熱します。温度管理が特に重要で、以下の項目に注意を払います。
• 予熱温度と時間の設定
• 本加熱温度のコントロール
• 冷却速度の管理
• 窒素雰囲気の維持
SMT実装が可能な部品
リード型部品
リード型部品は、基板との接続に金属製のリード(端子)を使用する部品です。視認性が高く、手作業での修正も比較的容易である特徴があります。
2方向リード(SOP、SSOP、SOJ)
- 部品の長辺2側にリードを配置
- 代表的な部品:SOP、SSOP、SOJ、SOT
- はんだブリッジのリスクが比較的低い
- 実装が容易で信頼性が高い
- 一般的に端子数が少ない用途に使用
4方向リード(QFP)
- 部品の4辺すべてにリードを配置
- 代表的な部品:QFP、QFJ
- 多ピン数に対応可能
- 高密度実装が可能
- はんだブリッジに注意が必要
リードレス型部品
外部リードを持たず、部品底面に直接端子を配置する部品です。小型化と高密度実装に適していますが、実装後の検査には特殊な機器が必要となります。
マトリクス型(BGA、CSP)
- 底面全体に格子状に端子を配置
- 代表的な部品:BGA、LGA、CSP
- 超多ピン部品に対応
- 最小ピッチでの実装が可能
- X線検査が必要
その他(CHP、QFN)
- 部品周辺部に端子を配置
- 代表的な部品:CHP、QFN、SON
- コンパクトなサイズ
- 中程度の実装密度
- 光学検査が可能
SMT実装時の不良と対策
はんだ付け不良
SMT実装において最も注意が必要なのが、はんだ付けに関連する不良です。代表的な不良の一つであるチップ立ち(マンハッタン)は、ランド面積やはんだペースト塗布量のバラツキが主な原因となります。この問題に対しては、予熱をする、はんだペースト塗布量を少なくする、ランド幅を小さくする、部品搭載の位置ズレを小さくすることが効果的な対策となります。
また、部品間隔が狭い基板や、はんだペースト量が過多な場合に発生しやすいはんだブリッジも重要な課題です。この問題を防ぐためには、設計段階での適切な部品配置の検討と、実装時の印刷条件の細かな調整が必要不可欠です。
はんだ欠けは、はんだペーストの不足や印刷ムラによって引き起こされる不良です。この問題の解決には、印刷条件の定期的な見直しに加え、メタルマスクの清掃を徹底することが重要です。さらに、リフロー工程での温度管理が不適切でフラックスが十分に効かず表面のはんだ粒が酸化するグレーピング(葡萄状化)については、温度プロファイルの最適化による予防が可能です。
部品実装不良
部品実装に関する不良も、SMT実装において重要な課題となっています。部品の欠落は、ピックアップミスや実装時の振動が主な原因です。この問題を防ぐためには、実装機の定期的なメンテナンスを行うとともに、部品の供給状態を常に適切に保つことが重要です。
極性の逆接続や方向の誤りは、プログラムミスや部品の誤装着によって発生します。これらの不良を防ぐためには、実装前の極性チェックを徹底するとともに、自動光学検査装置を導入して、実装後の検査体制を強化することが効果的です。
品質管理と検査体制
温湿度管理
実装品質を安定させるためには、作業環境の温湿度管理が不可欠です。特に以下の点に注意が必要です。
1. 温度管理
• 推奨範囲:20~28℃
• 変動範囲:±3℃以内
• 工程間の温度差管理
2. 湿度管理
• 推奨範囲:40~60%
• 結露防止対策
• 静電気対策との関連
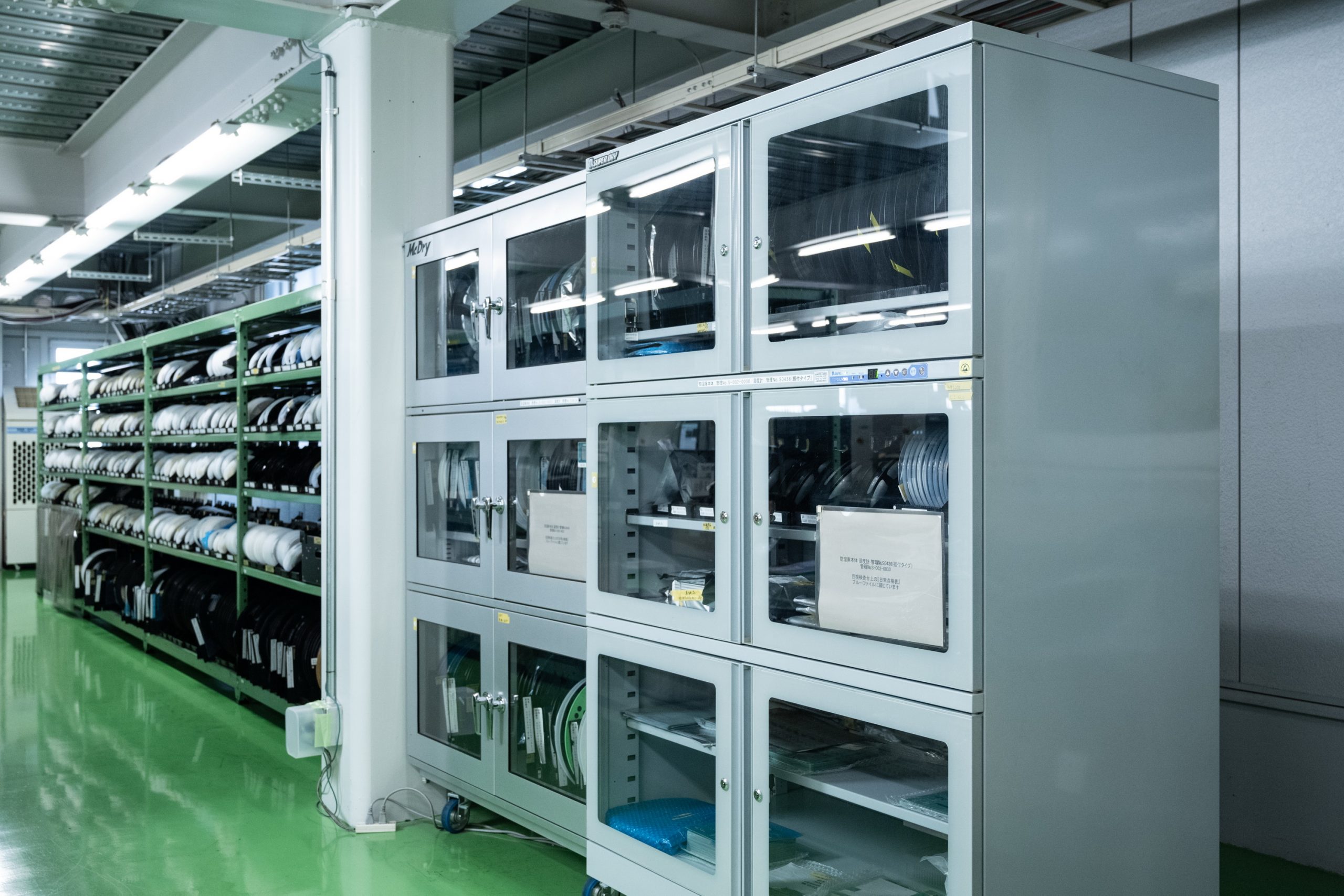
清浄度管理
微細な部品を扱うSMT実装では、清浄度管理も重要です。
1. パーティクル管理
• クリーンルームクラスの設定
• フィルター管理
• 作業者の入退室管理
2. 静電気対策
• 帯電防止床材の使用
• イオナイザーの設置
• 作業者の接地管理
外観検査
実装後の外観検査では、以下の項目を重点的にチェックします。
• はんだ付け状態
• 部品の位置ずれ
• 極性の確認
• 部品の欠落
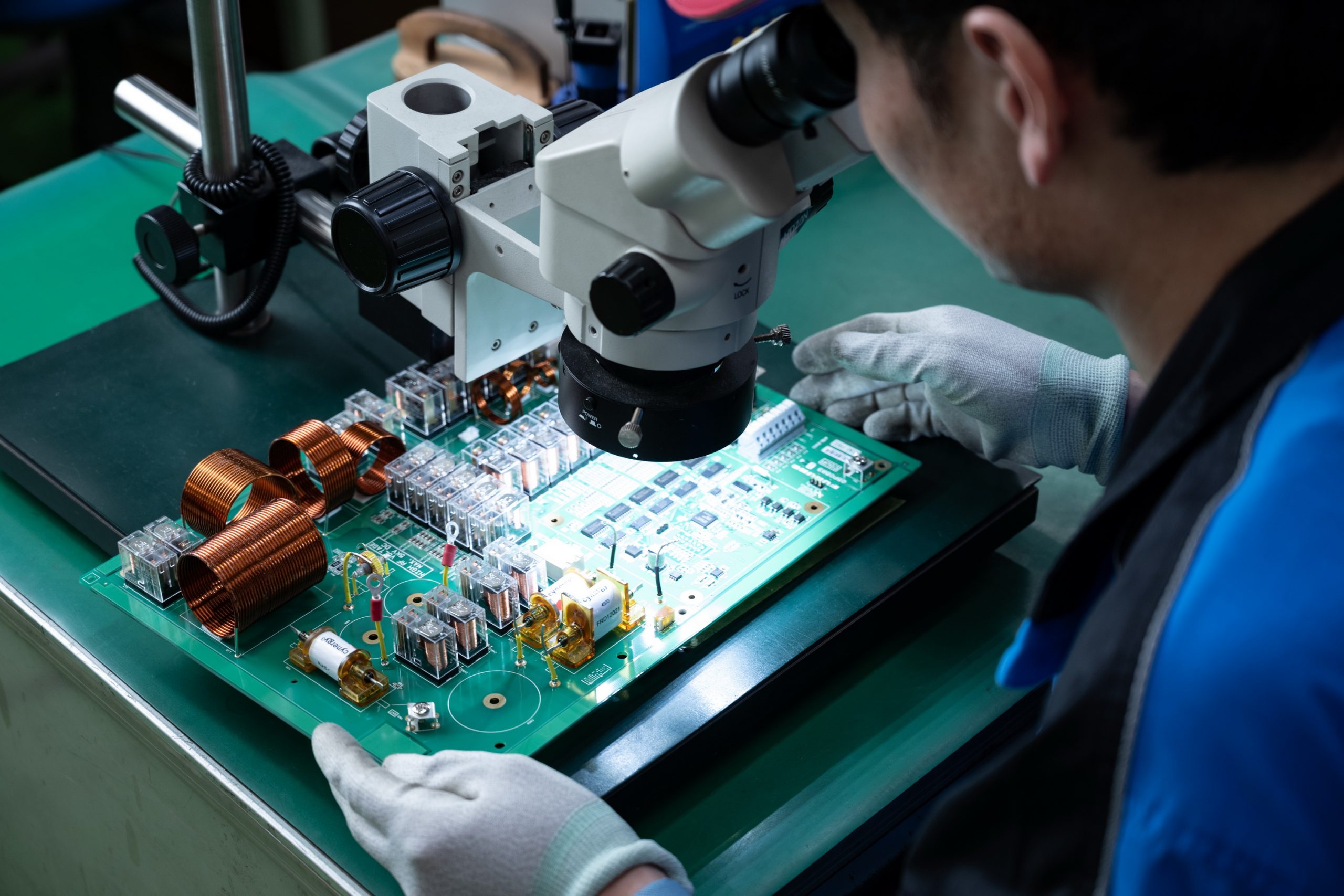
X線検査
BGAなどの底面端子部品の検査には、X線検査装置を使用します。
• はんだボールの接合状態確認
• ボイドの検出
• 内部断線の確認
• 異物混入の検査
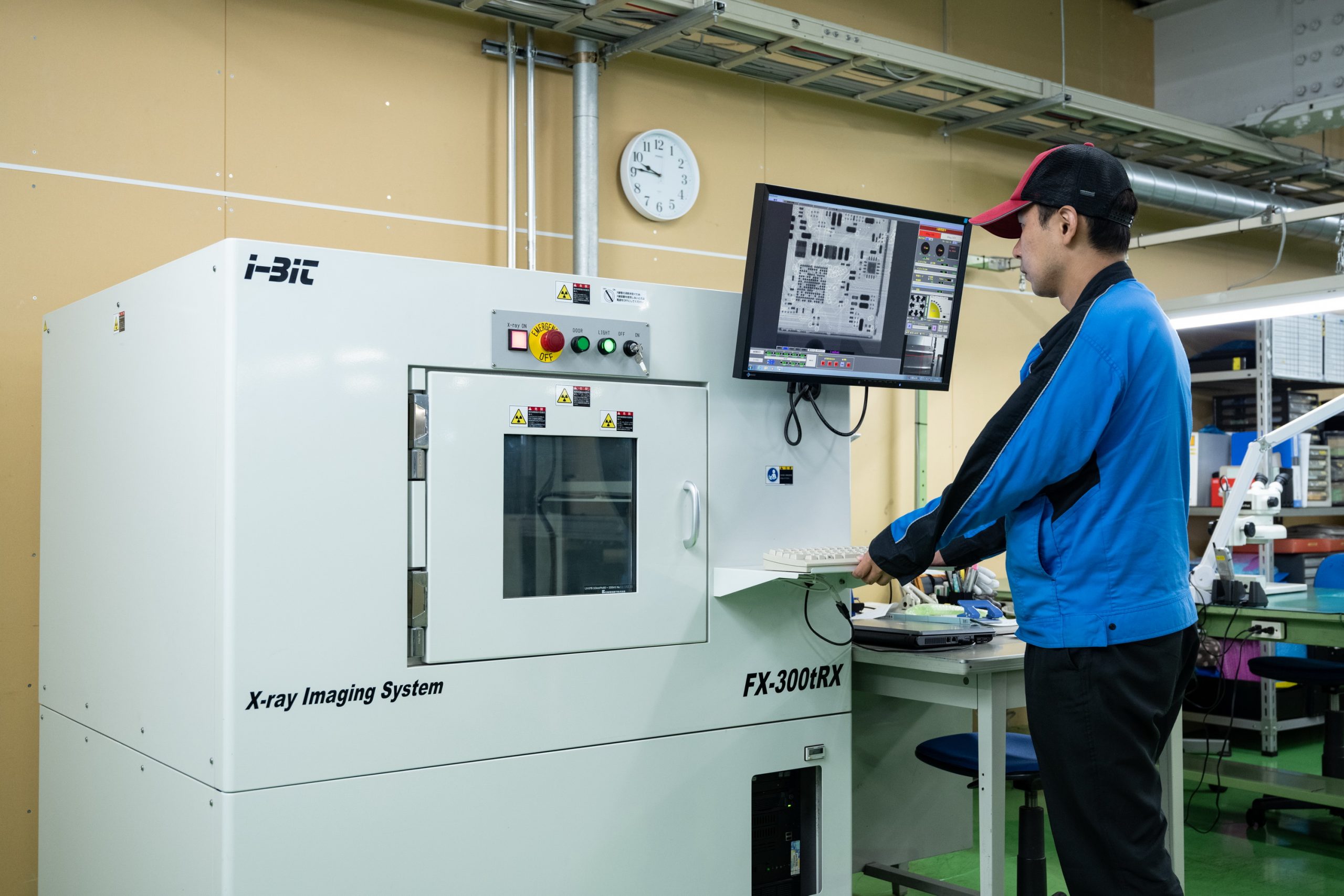
SMT実装業者選定のポイント
技術対応力
SMT実装業者を選定する際、最も重要な要素の一つが技術対応力です。実装可能な最小部品サイズや最小ピッチ、対応可能な基板サイズの範囲などを慎重に確認する必要があります。また、特殊部品への対応力も、製品の要求仕様によっては重要な選定基準となります。
品質管理体制
高品質なSMT実装を実現するためには、実装環境の管理が極めて重要です。温度、湿度、清浄度などの環境条件を適切に管理できる設備を有しているかどうかを確認する必要があります。また、外観検査やX線検査、機能検査などの検査体制も重要な評価ポイントとなります。
さらに、不良が発生した際のトレーサビリティ管理や対策プロセスが確立されているかどうかも、重要な判断基準です。これらの体制が整っていることで、問題発生時の迅速な原因究明と対策実施が可能となります。
前後工程の対応力
SMT実装工程の前後における対応力も、業者選定の重要な要素です。基板実装前の部品調達から、はんだ印刷工程の管理、リフロー後の検査工程、さらには修正・リペア対応まで、一貫した品質管理体制を持っていることが理想的です。
特に、部品調達における柔軟な対応力や、緊急時の修正対応能力は、製造における重要なファクターとなります。また、技術サポート体制や品質保証体制が充実していることも、長期的な取引を見据えた際の重要な判断材料となります。
納期対応力やコスト競争力も、実務的な観点から重要な選定基準です。市場の要求に応じて柔軟な対応ができ、かつ適切なコストバランスを実現できる業者を選定することで、持続的な生産体制を構築することができます。
SMT実装は現代の電子機器製造に不可欠な技術です。実装可能な部品の種類や特性を理解し、適切な実装方法を選択することが重要です。また、品質管理の観点から、実装業者の選定も慎重に行う必要があります。
実装時の不良を防ぐためには、設計段階からの配慮が必要で、部品選定、基板設計、実装条件の最適化など、総合的な取り組みが求められます。特に高密度実装や微細部品の実装においては、より高度な技術と管理体制が必要となります。
実装工程の各段階における適切な品質管理と、効果的な検査体制の構築が、高品質な製品製造の鍵となります。両面実装の活用や最新の検査技術の導入により、さらなる生産性向上と品質向上が期待できます。
基板の実装から組み立てまで一貫してお任せください
住本製作所では基板の実装(SMT・IMT)から組み立て、検査、梱包まで一貫して対応いたします。
業界・製品に合わせた対応や、中〜大型品の組み立ても可能ですのでお気軽にご相談ください。
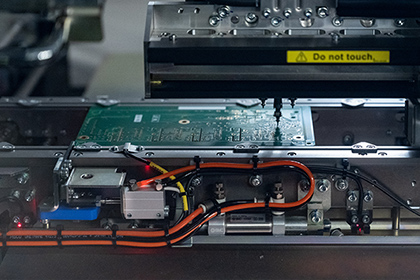
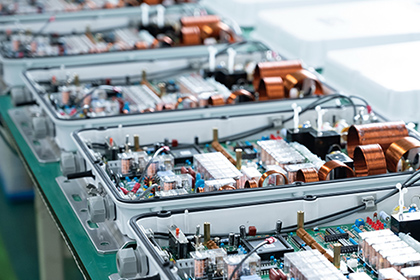
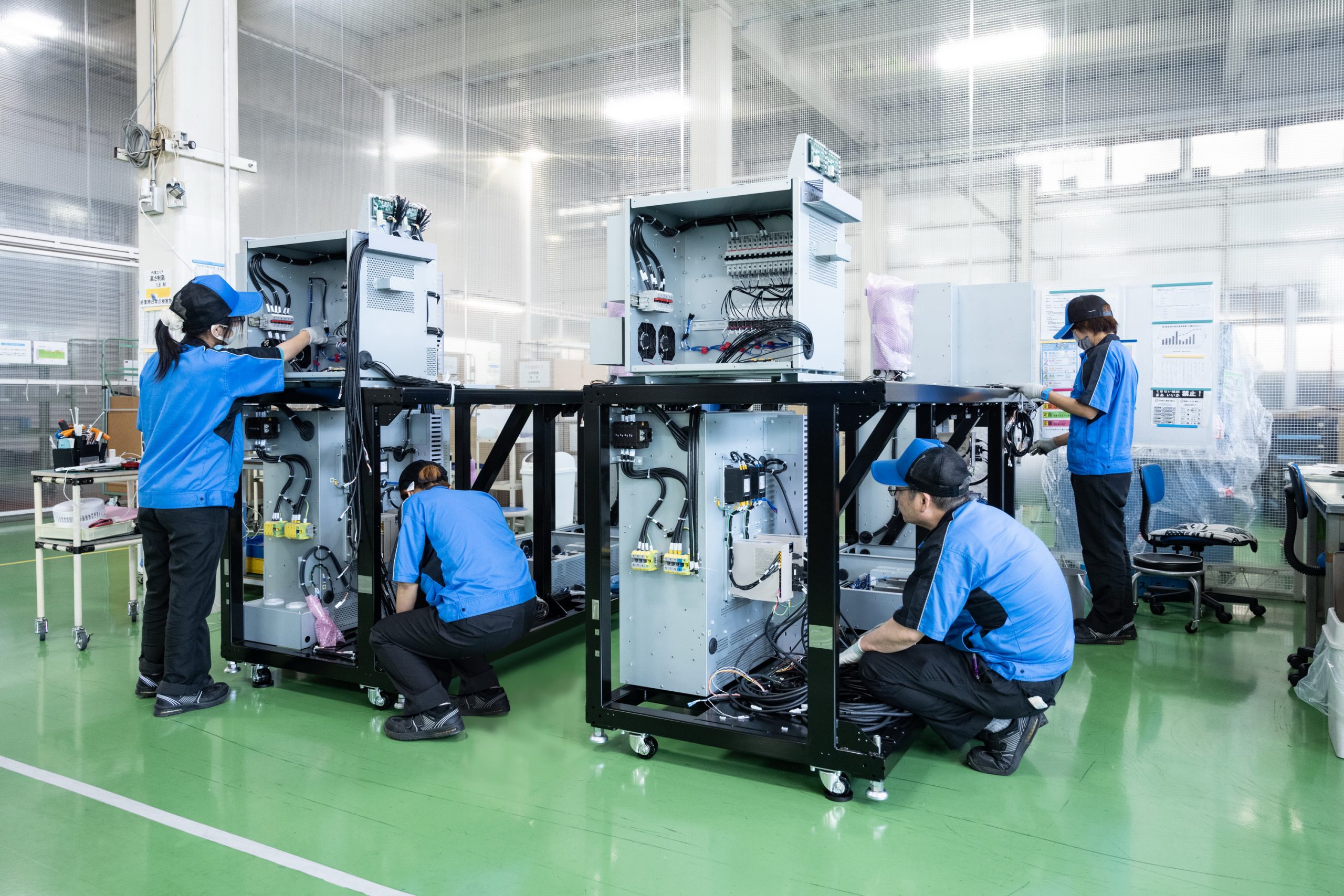